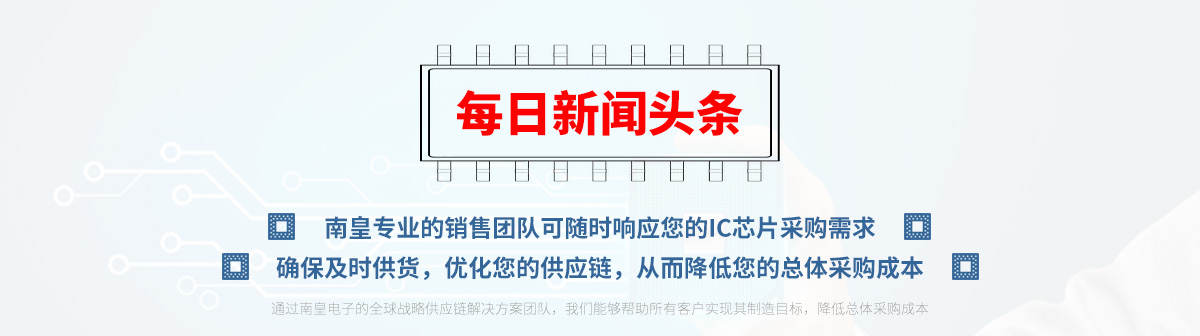
老少子化造成的缺工現象及covid-19疫情交叉影響,近期制造業經常受到外部環境快速變化的考驗,不僅造成供應鏈瓶頸,上游設備和零部件供應商也難以應對生產現場生產線的交通、調整和維護。卻也有PLC工業物聯網可支持邊緣工業物聯網OT IT信息,提供AI、Digitaltwins協助從智能工廠進步智能制造所需數據。
現在一般叫「智能工廠」管理模式是指通過收集和分析生產過程中的數據,如生產排程、機器作物動力等,探索生產面臨的瓶頸,克服過去難以量化的痛點。讓管理者優先解決問題,快速做出決策,減少生產現場浪費;然后利用有限的資源提高效率,降低成本。由于該模式相對簡單,效果明顯,中小企業進口門檻較低。
反觀「智能制造」,是硬件與軟件的合作,必須提前衡量客戶端的整體生產狀態,生產團隊還需要更高的管理能量和專業知識。通過傳感器,PLC收集生產數據,了解生產過程中的質量變化,使機器、接口設備和零部件能夠感知和控制,以保持質量的一致性。因此,發展瓶頸相對較深,仍依賴于研究機構和相關制造商的積極投資。
圖1 : 在這波數字浪潮下,工人應該如何工作?IT處理現場大量數字工具和管理能力FA還重視數據,降低運營風險。(source:cic.es)
幸運的是,這波疫情加速了生產現場的數字轉型(Digital Transformation;DX)如何進一步利用需求增加?IT數字工具及OT處理生產現場工廠自動化的管理能力(FA)大量數據;進而加強企業的彈性應變,降低經營風險的效果也備受關注。
三菱導入e-F@ctory架構 突出邊緣操作價值
日本品牌三菱電機由攝陽企業引進(Mitsubishi Electric)的FA最近積極推廣系列產品e@Factory以概念為核心的智能制造解決方案符合這一波數字轉型(DX)浪潮的背景主要來自于社會和商業環境的快速變化,必須為可持續發展做出貢獻,創造平衡工作滿意度和經濟發展的目標。
隨之推廣的DX戰略也不同于傳統歐美國家使用上層IT基于活用生產現場的數字模式來改善生產現場FA專業知識及OT再導入信息IT技術力求實現目標戰略。三菱強調:「重點是制造業只能利用其專有技術能力在生產現場實現DX,要真正在全球競爭中脫穎而出,而不是數字技術。」
三菱2003年公布的同因生產現場將繼續產生大量信息,難以實時上傳。e-F@ctory架構率先整合生產現場FA、Edge IT利用底層傳感器進行邊際操作技術,MELSEC系列PLC新一代工業網絡技術CC-Link IE TSN與不同合作伙伴合作的高速高效特點。
所有不同網絡的生產現場數據和信息都可以通過單的所有生產現場數據和信息,形成有意義的數據數據,上傳到控制層的集成控制和感知AOI設備和機器人將大大節省人力;甚至IT層的SCM/ERP系統管理供應鏈,一旦蜂鳴器發出警告并中斷生產,也可以分析和改進現場生產線,實現基于Edge的整體制造(monozukuri)優化解決方案。
圖2 : 三菱于2003年宣布e-F@ctory架構率先整合生產現場FA、Edge IT與不同合作伙伴合作的邊際操作技術。(source:tw.mitsubishielectric.com)
數字分身加值 催生節能智能工廠
目前三菱在名古屋新建廠房通過PLC收集生產、運營、質量等信息可視化,分析改進邊際運行,管理設備運行,排程和有效應用,促進生產設備與建筑設備合作優化工廠,追求生產設備高效運行和生產系統合作,避免材料或生產過程中止,減少產品質量損失。然后上傳服務器,然后通過運行管理監控機制與外部供應商生產管理監控系統的網絡合作,接受產品訂單準備,或根據生產進度和需要自動訂購零件不足的訂單。
而且因為是新建廠房,一定要兼顧ISO-利用14067節能等級PLC擔任主站(Master),副站及周邊空調、熱源及室外機、通風設備等(Salve)通信,監控實際生產運行狀態;添加變頻器、智能電表和傳感器,上傳數據進入SCADA實施可視化分析和改進,減少交流電源和通風設備的能耗。
只要有必要規劃智能工廠,最常見的兩個問題,包括:1。縮短設計時間,防止類似數據重復設置,一旦需要更改控制程序,仍需要時間輸入設置;2。現場調整時間較短。當設備啟動時,即使使使用3,也需要時間來解決設備之間的干擾問題D仿真器驗證,CAD與工程工具合作建立數字分合工程工具建立數字分體。
最新由三菱開發,即將上市的3D仿真器軟件「MELSOFT Gemini」,在引進或啟用生產設備之前,強調可以幫助客戶通過3D提高產能和質量的模擬技術。經過鏈接MELSOFT iQ Works軟件之一的MELSOFT Simulator,得以3D模擬生產設備上的可程控制器PLC、運動控制器等動作,如運動控制器和生產線的現狀。在加快和簡化客戶進口實體設備之前,優化從設計、制造到生產現場應用和維護的開發過程,不僅減少了生產過程中的碳排放,而且縮短了工作時間,提高了產品質量。
圖3 : 三菱即將上市的3D仿真器軟件「MELSOFT Gemini」,在引進或啟用生產設備之前,強調可以幫助客戶通過3D生產設備上的模擬、施工和驗證PLC、運動控制器等動生產線現狀。(souSiliconMotion代理rce:mitsubishielectric)
一旦導入設備出現異常,「驗證功能」即通過可程控器程序或波形分析異常原因,并用圖像確認動作,無需通過OPC可以連接服務器MELSOFT Simulator以及其他設備,縮短通信所需的時間D 數據更新頻率提高12倍,有助于降低重工,提高生產質量。
此外,MELSOFT Gemini還可以通過統計設備的運行狀態、操作人員的運行時間和待機時間,以及約2500種機械零件的圖形(e- Catalog),于3D將圖形和參數拖放在圖片上,繪制成各種圖表,簡單地構建生產線的布線設計。通過可視化圖表和統計功能,實現全面分析,識別產品率和設備運行率的變化,確認生產設備運行異常數據,使現場操作人員能夠快速找出異常原因,使生產線設計和改進更有效,未來三菱也將使用數字技術,致力于延續客戶業務的生命周期。
平臺集成硬軟件 融合OT IT信息
臺灣工業自動化大廠臺達電子公司(Delta)最近,它還發布了其智能制造業績,包括云服務、節能生產、自動化設備等智能制造應用,為客戶提供使用變頻器、伺服電機等高質量可靠的產品和解決方案PLC、完整的工控產品布局優勢,如傳感器和機器人。
同時,結合對市場的洞察,充分發揮自身生產線智能升級積累的豐富經驗,從下到上貫穿OT與IT層(制造管理和數據分析),整合自主開發的智能產品,規劃智能生產線和智能工廠;通過設備自動集成控制、制造生產管理平臺和戰爭中心、工廠能源監控系統,點、線、表面集成多個自動化系統,具備「立體維度」智能制造解決方案。
當今工業物聯網必然要有效融合OT IT其中,信息OT注重實時信息,包括事故報警、狀態監測、診斷干預等,使操作人員能夠提前維護或消除故障;同時,鏈接IT端實施質量管理、物流、訂單交易等信息,找出優化平臺整合信息,促進供應鏈實時響應,實施智能制造。
臺達最近發布的電子制造智能工廠解決方案采用自主開發的智能設備和智能生產線設計,導入DIAAuto設備自動化集成控制DIAWorks生產制造管理平臺,以及生產監控戰爭中心和智能工廠監控系統,通過實時收集生產信息,完善人員、機器、材料、方法、環、測量生產、質量、設備和倉儲管理。
圖4 : 臺達最近發布的電子制造智能工廠解決方案通過在自己的生產領域驗證和積累成功經驗,建立了一個標準化的相關軟件平臺,并結合智能設備PLC(攝影:陳念舜)
建立標準化相關軟件平臺,結合底層智能設備,通過在自己的生產領域驗證和積累成功經驗PLC通過DIALink設備網絡平臺和系統內部建設的設置模式使用戶能夠輕松連接設備數據;支持 MODBUS、OPC生產現場常用的通信標準,整合性高,兼容性強。邊緣層Edge則透過DIABCS控制和控制整線設備DIAEAP設備自動控制兩套系統,M整合異質設備M2M交互和數據處理和轉換不僅可以在異常情況下發出命令,還可以根據不同的應用需求將系統實時操作分析轉化為有用的洞察力,提供上層系統「即取即用」。
芯片采購網專注于整合國內外授權IC代理商現貨資源,芯片庫存實時查詢,行業價格合理,采購方便IC芯片,國內專業芯片采購平臺。
導入先進AIoT技術 從智能工廠到智能制造
值得一提的是,三菱目前已經引進了先進的技術DX層次,也分別使用:「行動DX」克服勞動力短缺問題,通過與生產在線機器人的合作/自動化,人們可以擺脫單調的工作,從事高附加值的工作;「知識DX」,促進員工和三菱原創的人工智能技術(Maisart AI)合作,通過深度/強化學習和大數據分析能力,任何人都可以繼承熟練工人的知識和技能,減輕現場操作負擔和時間成本。同時強調其屬性compact AI技術,可導入三菱FA領域知識;同時利用三菱Edge簡化數據收集過程,加快建設和完善產品AI系統。
圖5 : 目前,三菱已經引進了先進技術DX也促進了員工和原創人工智能技術(Maisart AI)同時強調合作屬于compact AI技術,可導入三菱FA領域知識;同時利用公司Edge簡化數據收集過程,加快建設和完善產品AI系統(攝影:陳念舜)
三菱進一步指出,目前行業需要實施DX的關鍵詞為「開放」,也就是說,基于客戶不僅會選擇單一的系統集成商和網絡,而且很容易在生產現場遇到網絡、系統和數據分散的結果,幸運的是e-F@ctory加快開放式轉型FA設備合作與創新,進而導入Maisart AI、EDGECROSS技術,并于2011年宣布成立e-F@ctory Alliance2018年發布開放網絡CC-Link IE TSN統一智能工廠架構。
為了適用于DX制造業時代靈活先進,三菱必須提供超越公司和行業傳統邊界的空間,在邊際運算領域建立空間EDGECROSS由于現場通信標準不同,軟件平臺難以解決IT軟件和設備鏈接的問題使任何人都能在工業計算機上運行可視化邊際應用軟件,通過在該領域的競爭與合作,收集不同的網絡數據進行統計和分類,促進更有效的利用。
- 富士康于明年第一季度開始生產自動駕駛電動拖拉機訂單
- 滿滿的知識點|關于射頻微機電系統開關的事情
- 聯想凌拓和Veritas合作推出企業級備份解決方案,護送數智世界
- 張翔:發達國家正成為中國汽車出口的主要市場
- 擴大西部數據WD_BLACK SSD產品組合,滿足各類游戲玩家的多樣化需求
- 卓勝微:芯卓半導體卓半導體產業化建設項目濾波器產品小批量生產
- 萬萬沒想到,NFT日常應用這么多!
- 研華發布兼容性NVIDIA Jetson的AI邊緣智能系統EPC-R7200
- 羅德和施瓦茨推出了新的戶外頻譜監控和無線電定位解決方案
- 45.98 萬元,理想 L9 旗艦 SUV 正式發布:1315km 綜合續航,零百加速 5.3s
- 華為發布All-Band 5G全系列解決方案
- 這些上海芯片公司開始復工復產,確保芯片持續供應
